Standard series test weights are manufactured with a high level of precision and accuracy to ensure their reliability in calibration and measurement applications. The materials used in their construction play a crucial role in achieving this precision. Here's an overview of how standard series test weights are typically manufactured and the common materials used:
1. Material Selection:
The choice of material is a critical factor in the construction of standard series test weights. Common materials used include:
Stainless Steel: Stainless steel is a popular choice due to its corrosion resistance, durability, and consistent density. It is often used for precision test weights.
Cast Iron: Cast iron weights are also common, known for their stability and cost-effectiveness. They are often used for heavier weights.
Brass: Brass is used for weights that require non-magnetic properties and are less prone to corrosion. It is often used for smaller precision test weights.
Aluminum: Aluminum test weights are lightweight and non-corrosive, making them suitable for various applications.
Zinc: Zinc weights are used for applications where cost is a significant factor. They are less expensive but less durable than other materials.
2. Precision Machining:
The selected material is precision-machined to create the desired weight shape and size. Machining ensures that the weight's mass is distributed evenly for consistent results.
3. Calibration and Certification:
After machining, test weights undergo a calibration process. The weights are compared against a reference standard to ensure their accuracy. Once calibrated, the weights are certified and labeled with the appropriate class or accuracy designation.
4. Traceability:
The calibration and manufacturing process includes establishing traceability to national or international standards. This means that the weights' measurements can be traced back to a recognized standard, ensuring their reliability.
5. Adjustment Cavities: Some precision weights have adjustment cavities or cavities that can be filled with a material of known density to fine-tune the weight's accuracy.
6. Surface Finish:
The surface of the weight is typically finished to minimize any surface imperfections or irregularities. This helps ensure that the weight's mass is evenly distributed.
7. Markings and Certification:
Standard series test weights are typically marked with their weight value, material type, and any relevant certification information. These markings provide important information to the user.
8. Protective Coatings:
Some weights may receive protective coatings or finishes to enhance their durability, prevent corrosion, or reduce wear and tear.
It's important to note that the manufacturing process must adhere to strict quality control standards to produce test weights with high accuracy and precision. The choice of material depends on the intended use, environmental conditions, and the required accuracy level. Proper care and handling of test weights are also crucial to maintaining their accuracy over time.
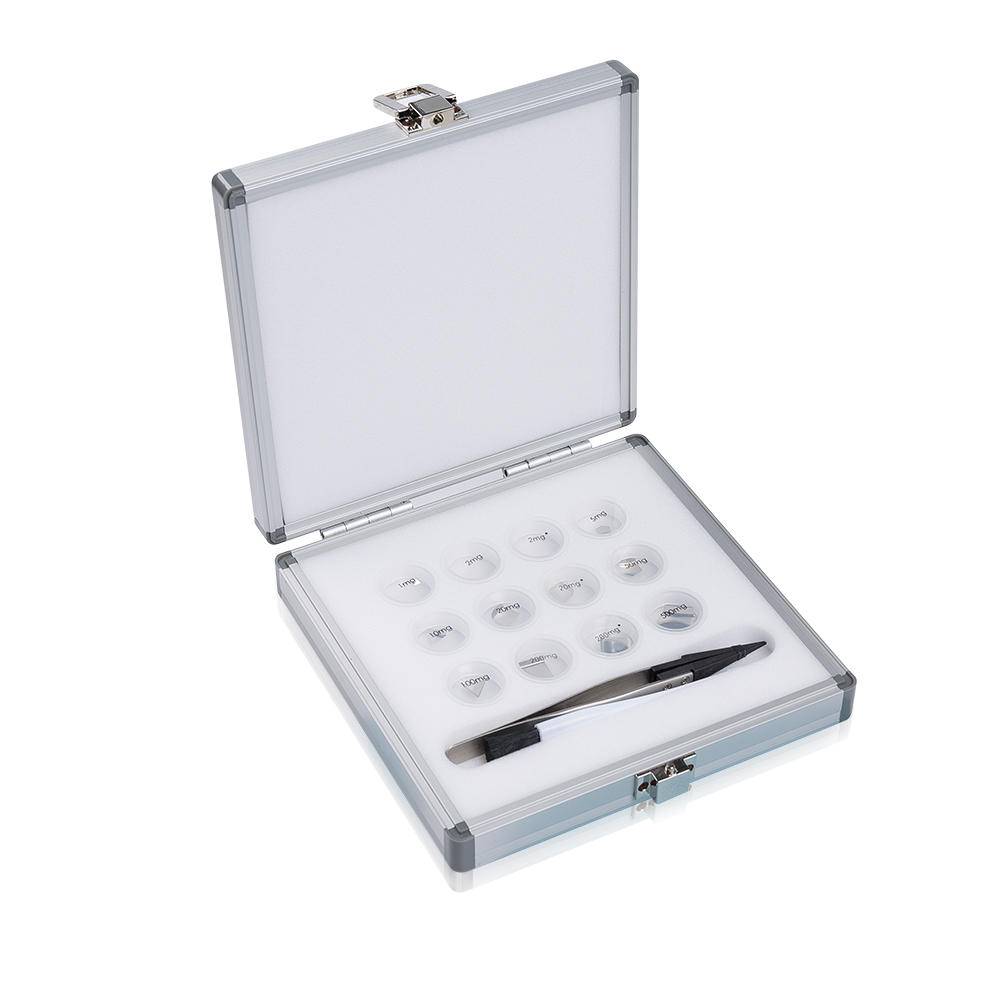
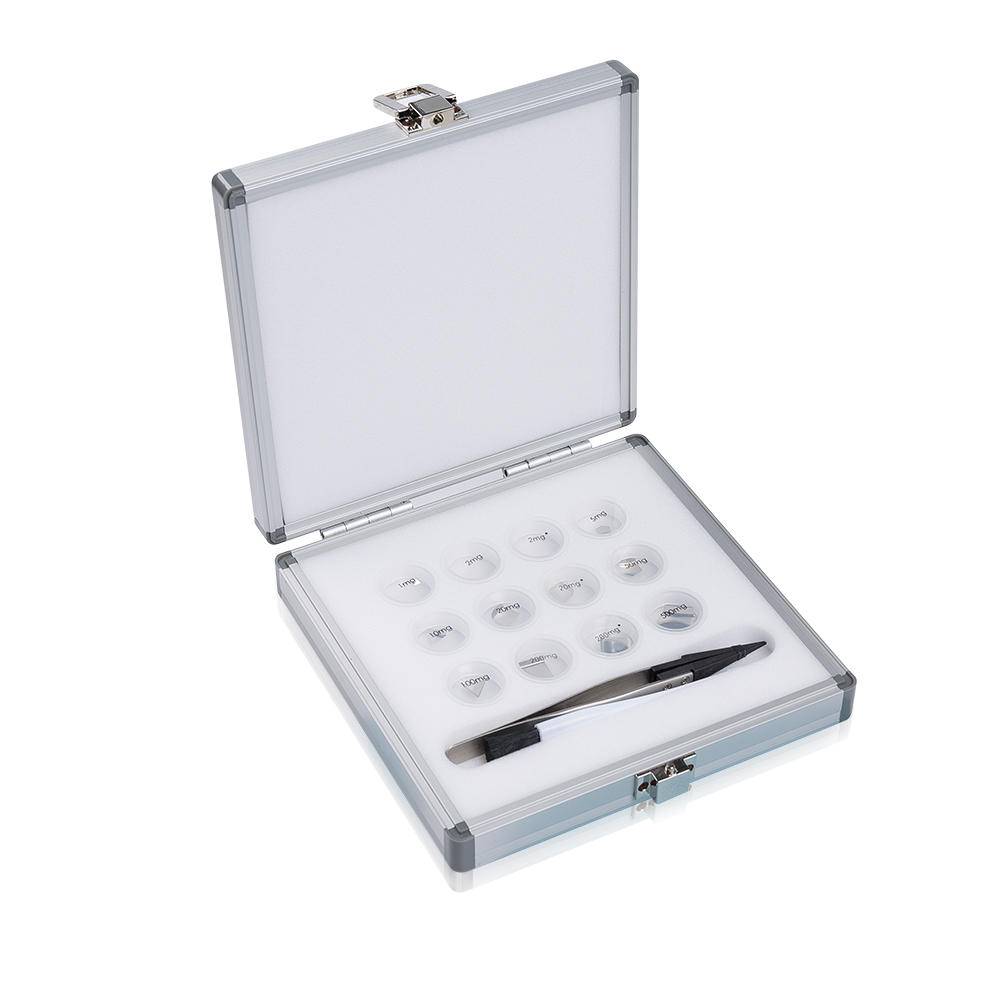